Inverter Maintenance and Repair – Premier Service at KTH ELECTRIC
“Facing issues with your inverter? Don’t hesitate! Let KTH ELECTRIC be your partner with professional maintenance and repair services. Contact us today at Hotline: +84-968-27-1199 for free consultation and immediate support!”
Inverters are critical components in industrial electrical systems, ensuring stable production line operations, motor speed regulation, and energy savings. Regular maintenance and repair are essential for optimal performance. At KTH ELECTRIC, we provide professional inverter maintenance and repair services delivered by experienced engineers.
Why Regular Inverter Maintenance is Essential
- Ensure optimal performance: Regular maintenance optimizes the system’s operational efficiency.
- Prevent breakdowns: Timely detection and resolution of technical issues before major failures occur.
- Save costs: Reduce major repair expenses and production downtime.
- Extend equipment lifespan: Periodic maintenance prolongs the life of the inverter and related components.
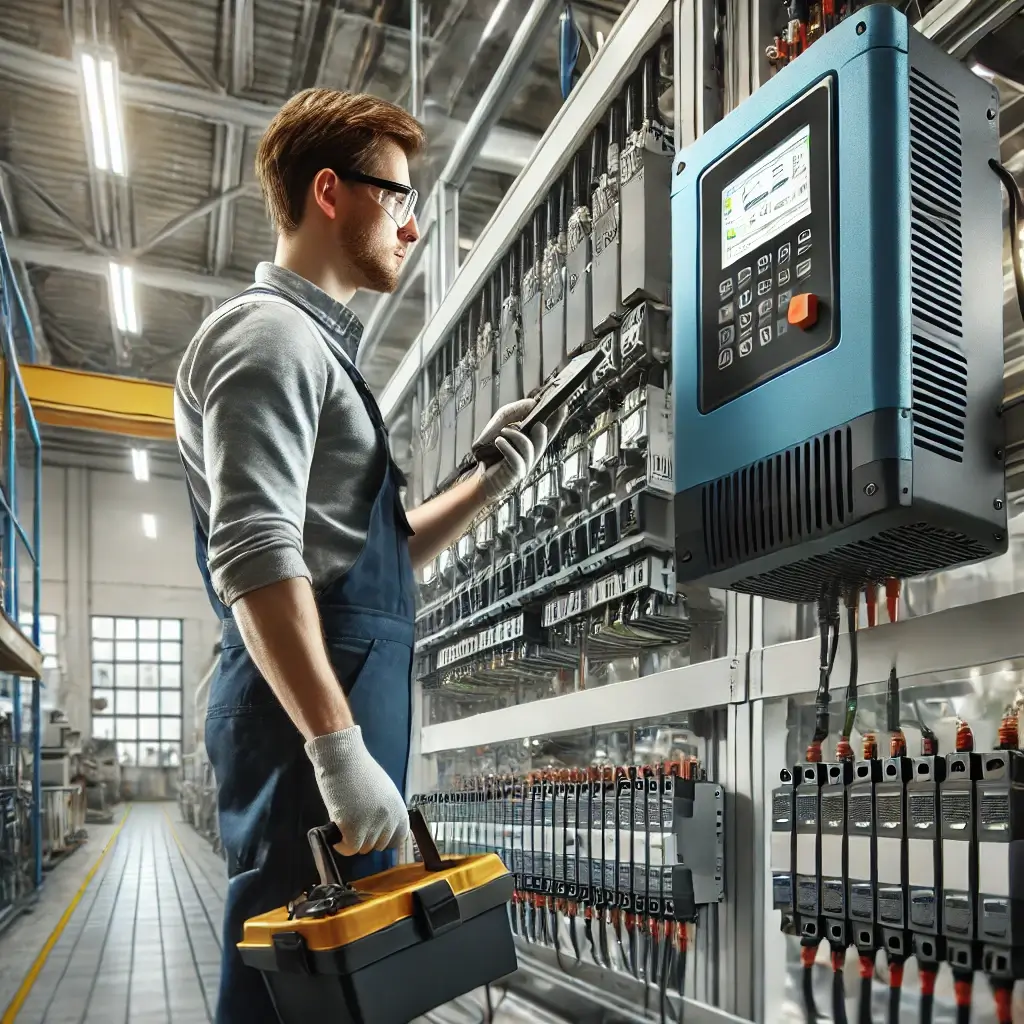
The Importance of Regular Inverter Maintenance
Regular maintenance minimizes risks, saves costs, and extends inverter lifespan. Below is a detailed comparison table:
Factor | With Regular Maintenance | Without Maintenance |
---|---|---|
Failure rate | Reduced by 80% | Increased by 60% |
Unexpected repair costs | Low | High |
Inverter lifespan | Extended by 30% | Reduced by 40% |
Operational efficiency | Stable | Frequently interrupted |
Productivity risk | Significantly reduced | High |
Supported Inverter Brands
KTH ELECTRIC provides maintenance and repair services for top inverter brands, including:
- ABB
- Siemens
- Schneider Electric
- Mitsubishi Electric
- Delta Electronics
- Fuji Electric
- Yaskawa
- Omron
- Danfoss
- Hitachi
Inverter Maintenance Process at KTH ELECTRIC
1. Initial Assessment
- Comprehensive inspection of the inverter and related electrical systems.
- Use of specialized equipment to measure and verify technical parameters.
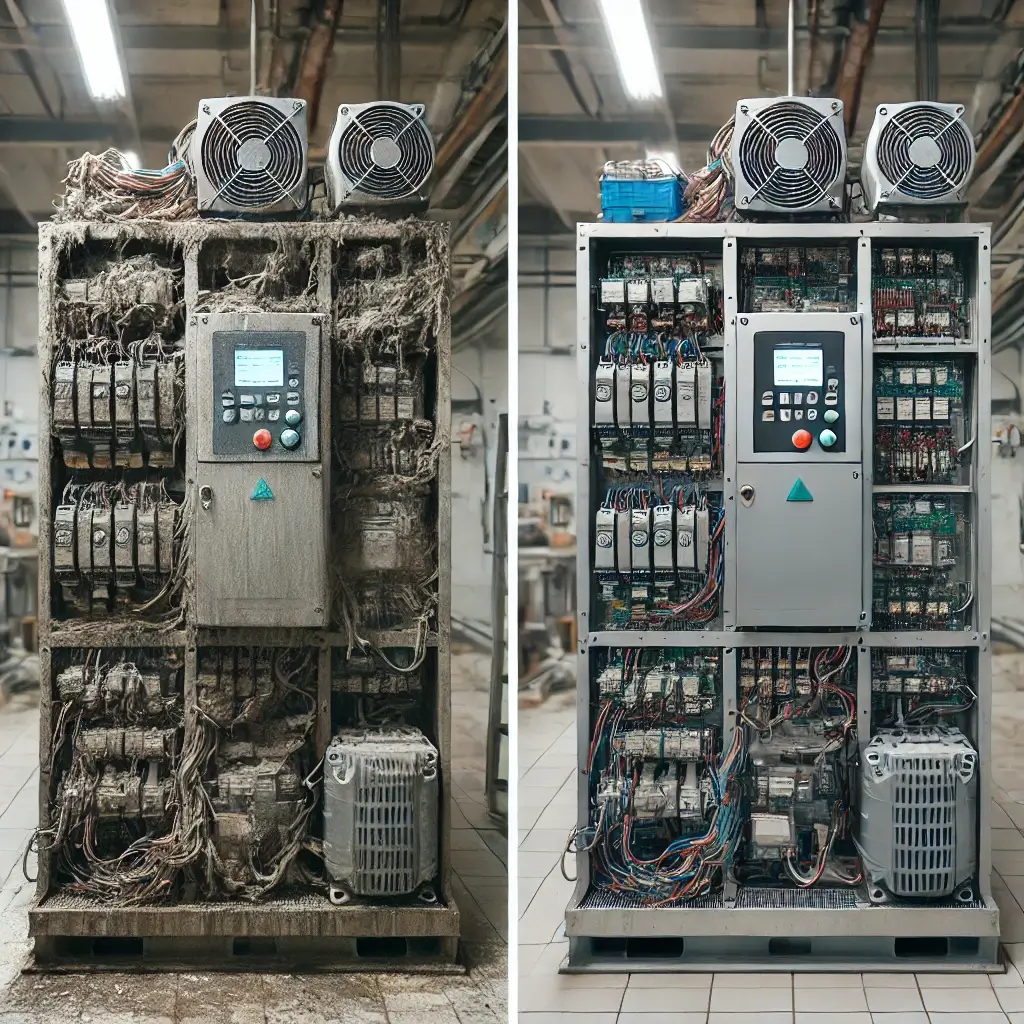
2. Cleaning and Dusting
- Remove dust and debris from circuit boards, cooling fans, and other components.
- Use specialized solutions to clean electrical contact points.
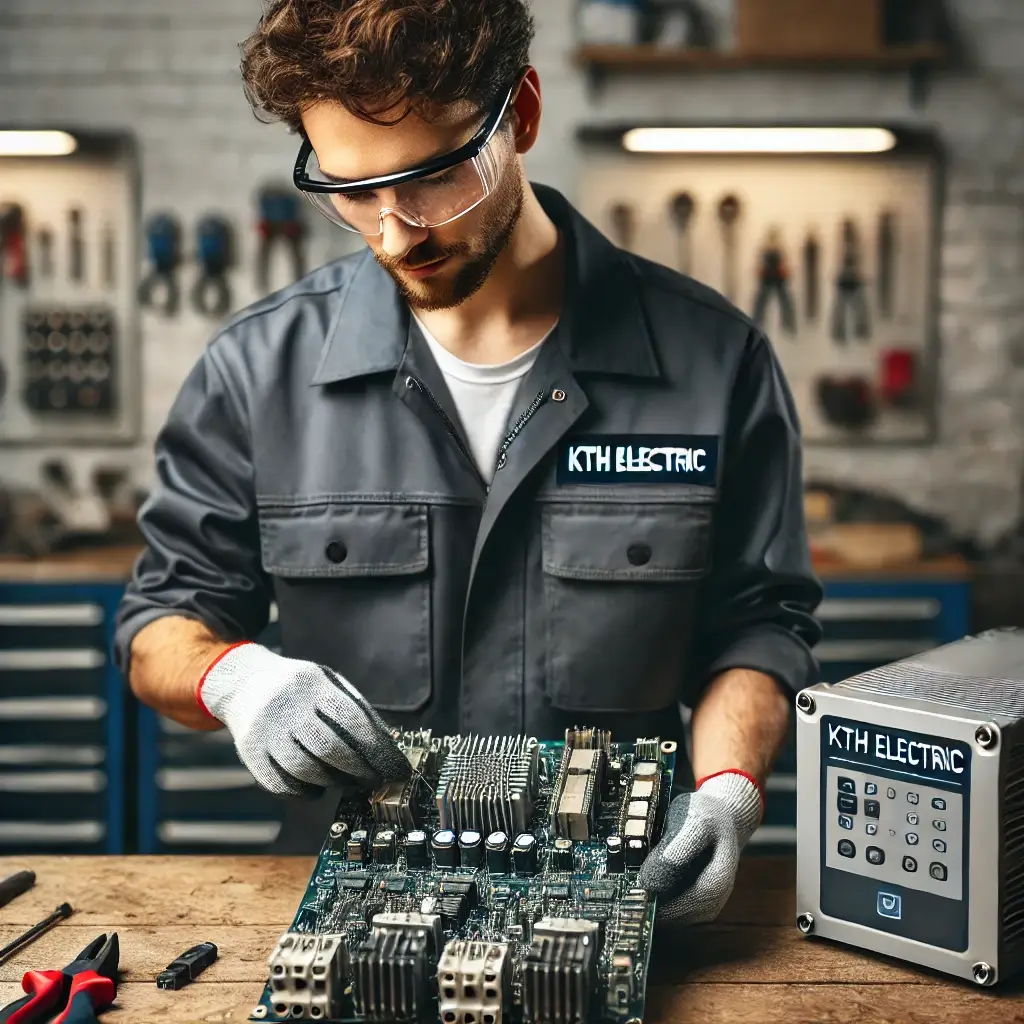
3. Detailed Checks
- Measure insulation resistance, voltage, and load current.
- Inspect components such as capacitors, IGBTs, SCRs, and diodes.
- Use thermal cameras to identify abnormal hotspots.
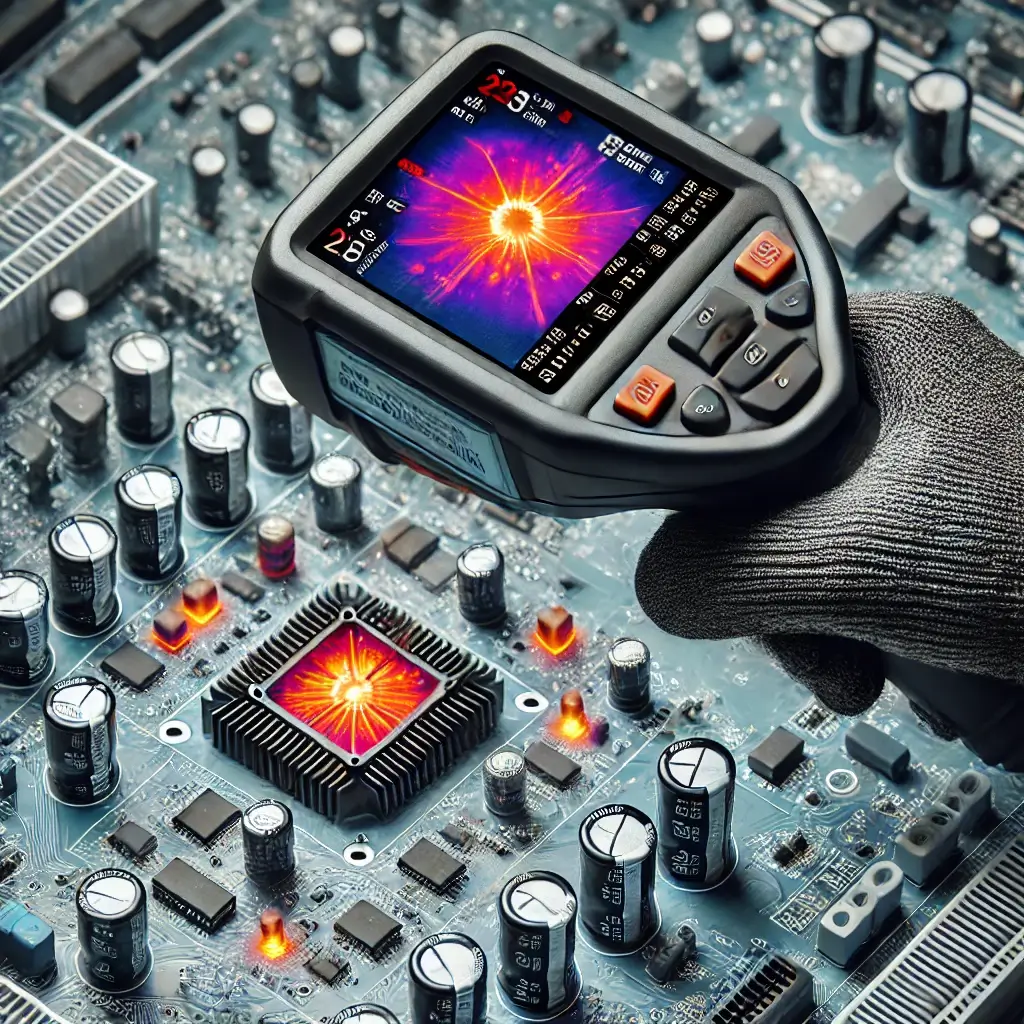
4. Repairs and Replacements
- Replace faulty components such as cooling fans, capacitors, or damaged boards.
- Update software or reconfigure settings as required.
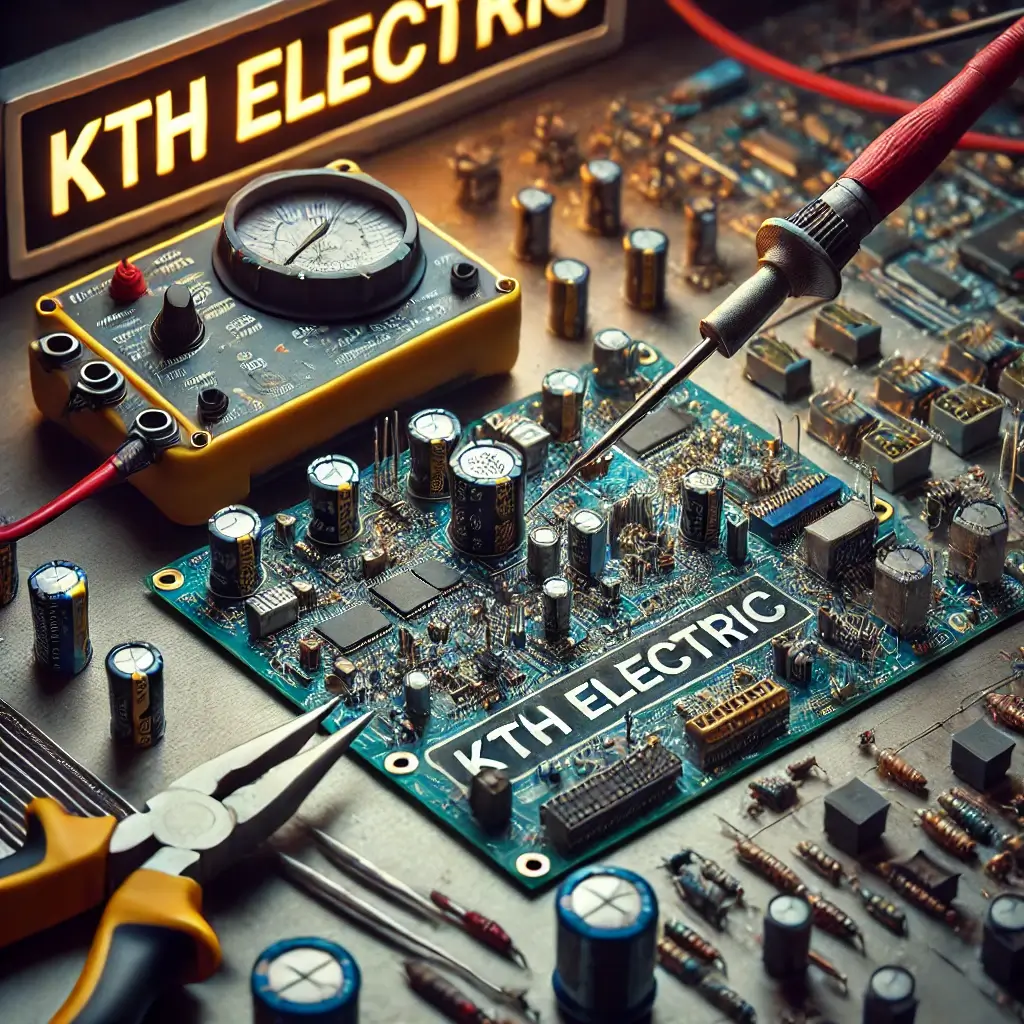
5. Final Inspection and Handover
- Reinspect the entire system to ensure stable inverter operation.
- Prepare detailed reports and hand over the equipment to the customer.
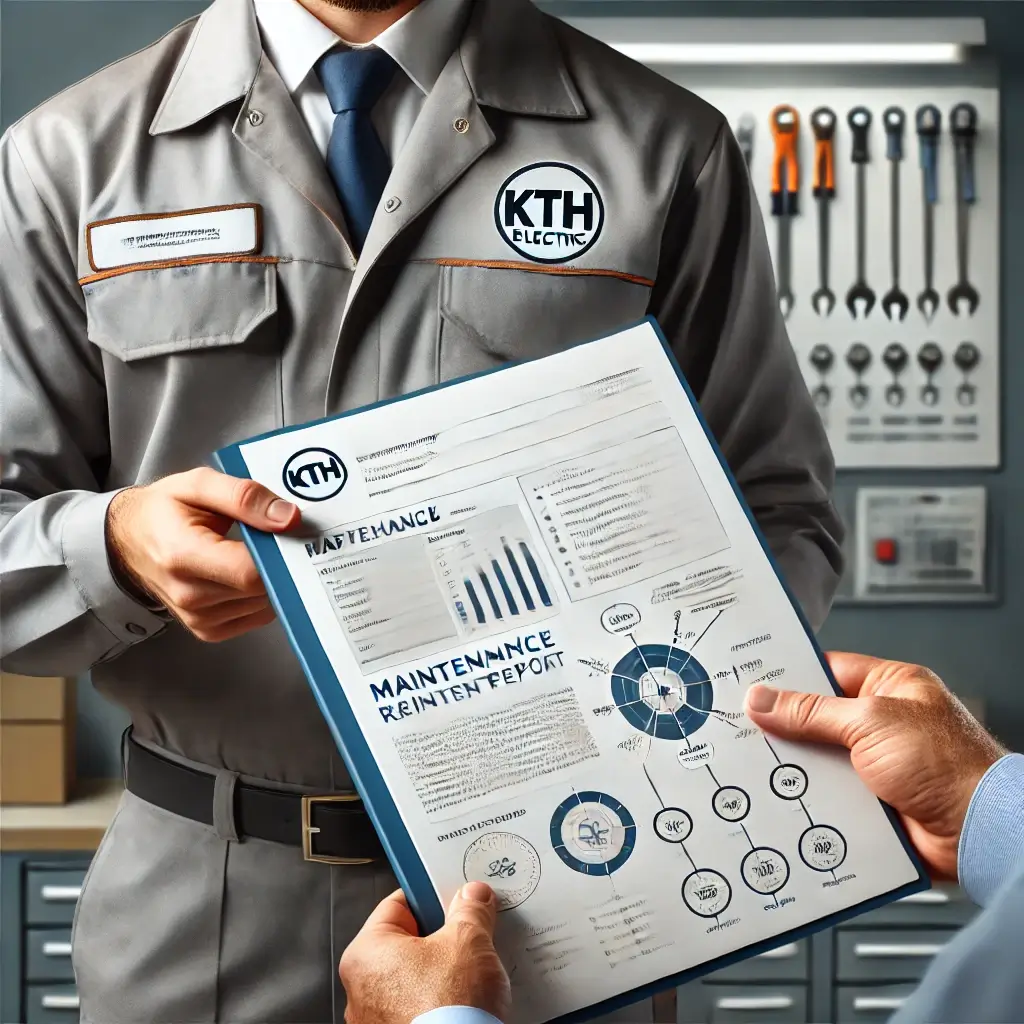
Common Inverter Issues
Inverter Issue | Cause | Solution |
---|---|---|
Overheating | Cooling system blockage | Clean fan and air filters |
Overcurrent | Motor overload | Inspect power cables and motor |
PCB malfunction | Moisture or dust | Clean and replace components |
Phase loss | Broken wire, loose connection | Inspect and reconnect power cables |
Power supply failure | Faulty capacitor or fuse | Inspect and replace damaged components |
Contact Us
Get in touch with KTH ELECTRIC for free consultations and detailed quotes for inverter maintenance and repair services. We guarantee optimal and efficient solutions for your industrial electrical systems.
Hotline: +84-968-27-1199 | Email: contact@kth-electric.com | Website: KTH ELECTRIC