Low Voltage Electrical Cabinet Maintenance: Enhancing System Efficiency and Safety
Looking for a reliable solution for low voltage switchgear maintenance?
Let KTH ELECTRIC assist you! With experienced technicians and modern technology, we guarantee:
✔️ Comprehensive inspections
✔️ In-depth maintenance
✔️ Standardized testing
✔️ Fast support
Contact us now for free consultation and the best maintenance solution for your system!
📞 Hotline: +84-968-27-1199
📧 Email: info@kth-electric.com
🌐 Website: kth-electric.com
Don’t let unexpected issues disrupt your operations! Take action today to ensure the safety and maximum performance of your electrical system!
The Importance of Preventive Maintenance
Preventive maintenance is essential in managing industrial electrical systems. Scheduled maintenance based on cycles or manufacturers’ technical standards not only reduces the risk of failures but also maintains performance and extends equipment lifespan.
Standard Low Voltage Switchgear Maintenance Process
1. Overall Inspection
- Identify abnormalities such as overheating, unusual noise, or burning smells.
- Check the condition of cable connections to ensure there is no damage or looseness.
- Measure the insulation resistance of devices to evaluate insulation capacity.
2. Cleaning and Dusting
- Remove dust using vacuums, cloths, or alcohol-based solutions.
- Treat corrosion on busbars and metallic components.
3. Device Checking and Testing
- Measure contact resistance of devices like Contactors, MCCBs, and busbars.
- Test the functionality of ATS and overcurrent relays.
- Test critical components such as circuit breakers and capacitor banks.
Benefits of Regular Maintenance
- Ensure Safety: Reduce risks such as fire or electrical leakage, protecting operators and equipment.
- Prolong Equipment Lifespan: Maintain stable performance, minimize wear, and extend the device’s lifecycle.
- Cost Savings: Detect potential issues early, minimizing unexpected repair costs and downtime.
Common Faults and Prevention Methods
Common Issues:
- Oxidized Contacts: Reduces electrical conductivity and causes overheating.
- Faulty Protective Relays: Fails to detect overloads or short circuits in time.
- Broken or Loose Connections: Risks short circuits or power loss.
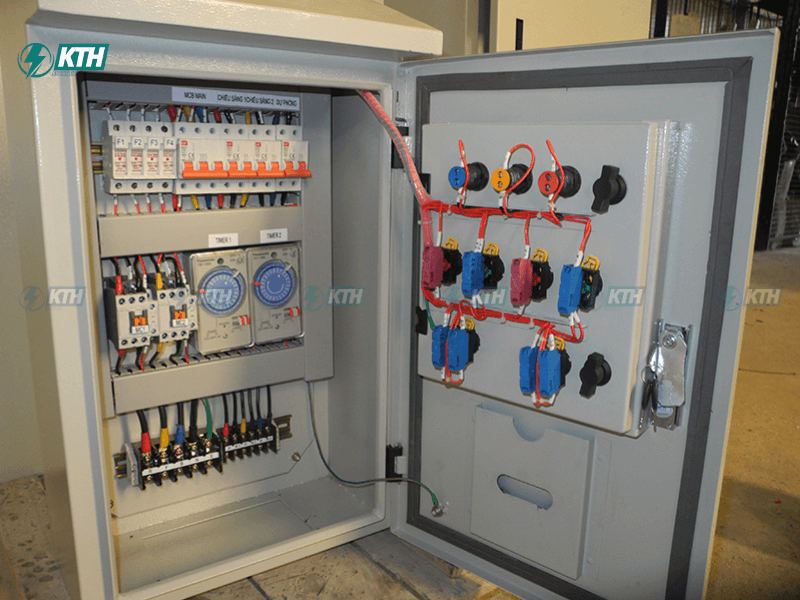
Common faults in low voltage switchgear components like overloads, short circuits, and poor contacts. Contact KTH ELECTRIC for quick support and resolution.
Prevention:
- Perform regular maintenance to clean, inspect, and replace components as needed.
- Use specialized testing equipment to detect faults early.
Detailed Device Inspection Guide
Device | Inspection Details |
---|---|
Contactor | Check contacts to ensure they are not worn or stuck. |
ATS | Evaluate automatic transfer functionality between main and backup power sources. |
MCCB | Measure opening/closing times and contact resistance between poles. |
Busbars | Check tightness, measure insulation resistance, and treat corrosion if present. |
Protective Relays | Test functions like overcurrent and ground fault protection to ensure accurate response. |
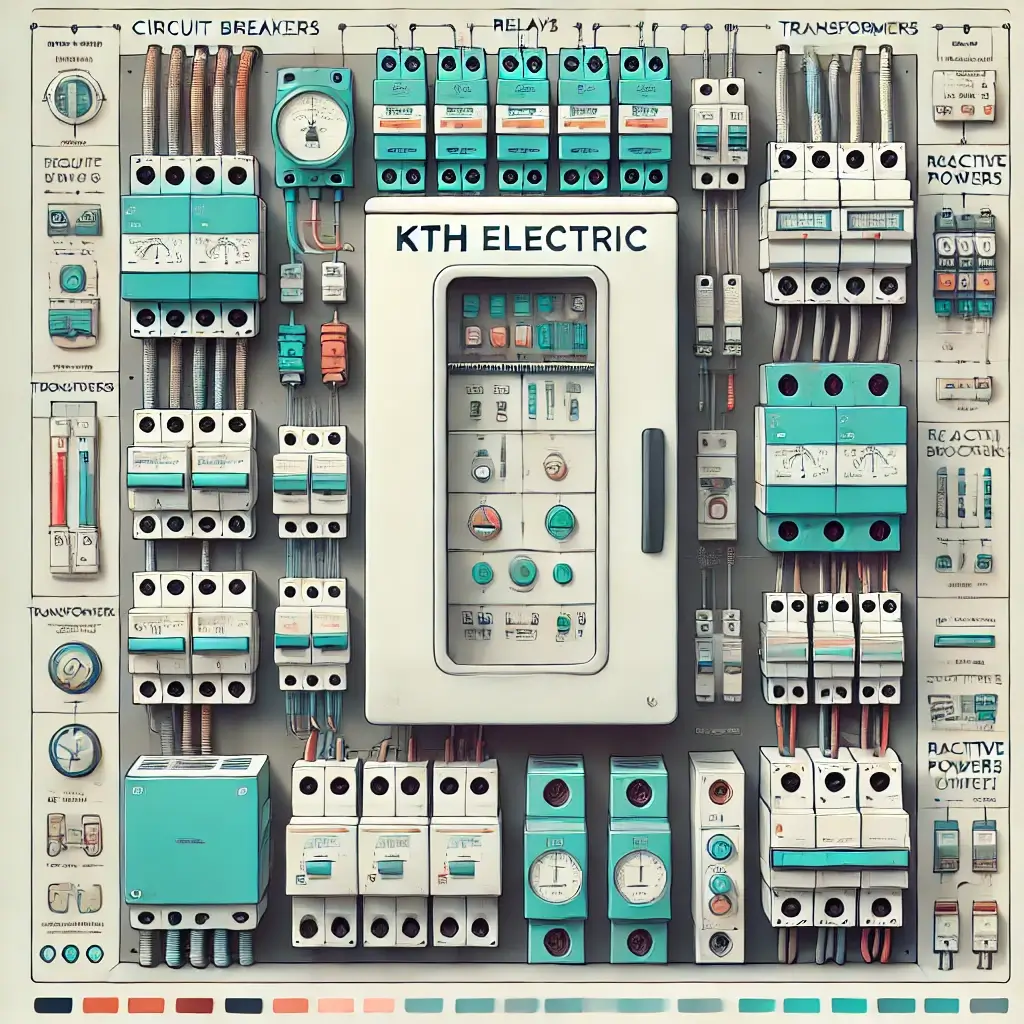
Illustrated guide: Annotated diagram of switchgear components for detailed maintenance.
Maintenance Frequency Based on Usage
System Type | Recommended Frequency |
---|---|
Large Industrial Systems | Quarterly inspections and maintenance to maintain stable performance. |
Office Systems | Routine checks every 6 months for moderate operation needs. |
Continuous Operation Systems | Flexible maintenance schedules for signs of issues or specific requirements. |
In-Depth Testing Procedures
1. ACB/MCCB Testing
- Insulation Resistance Testing: Verify insulation capacity between poles per manufacturer standards.
- Contact Resistance Testing: Ensure minimal and uniform resistance values across poles.
- Voltage Withstand Testing: Assess insulation endurance under specified voltage for one minute.
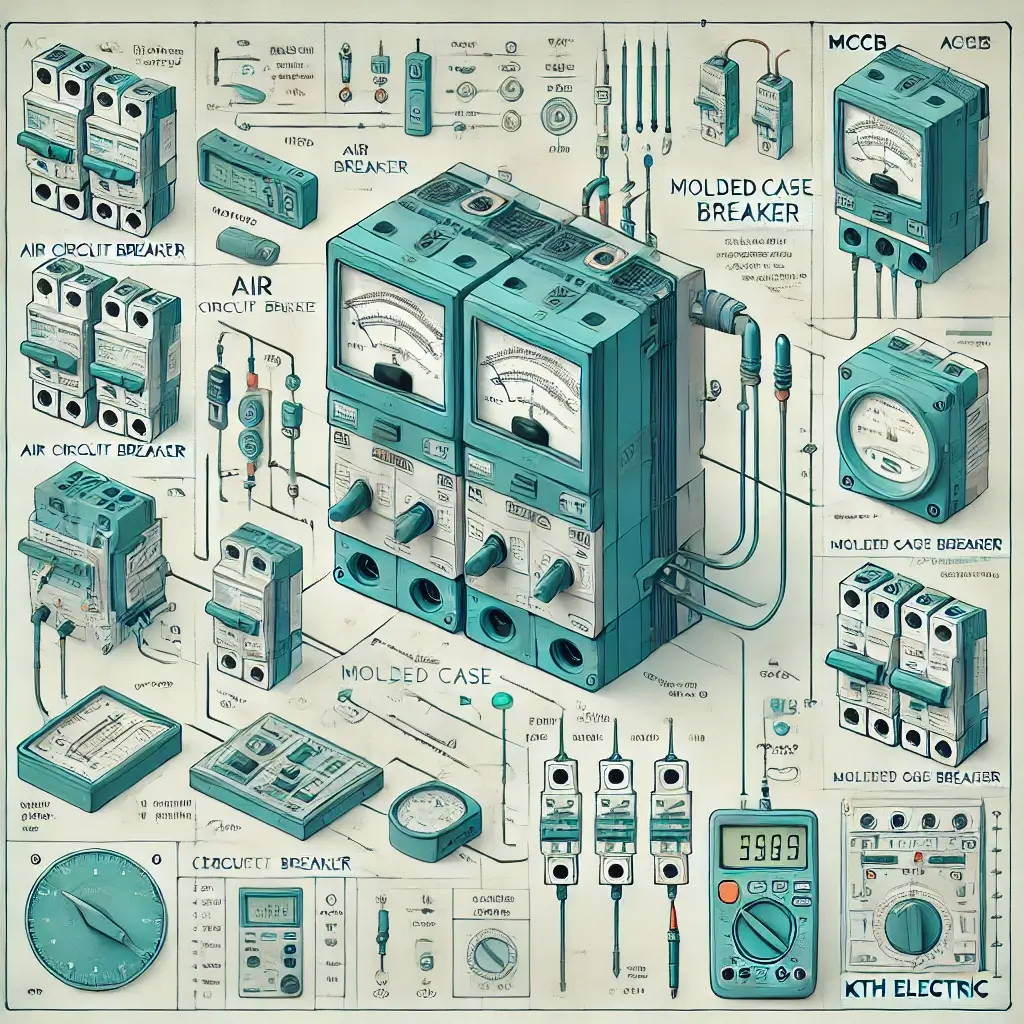
Illustration: Detailed ACB and MCCB testing procedures designed by KTH ELECTRIC, highlighting measurement parameters and precise execution steps.
2. Protective Relay Testing
- Overcurrent Testing (50/51): Ensure accurate tripping under overcurrent conditions.
- Ground Fault Testing (50N/51N): Evaluate protection capabilities during leakage currents.
Why Choose KTH ELECTRIC for Low Voltage Switchgear Maintenance?
-
<