Transformer Station Maintenance Service
Why is Transformer Station Maintenance Essential?
Transformer stations are the core of energy distribution, ensuring the stable conversion and delivery of electricity to industrial systems and equipment. Without regular maintenance, transformer stations are susceptible to issues such as overloading, oil leakage, and relay malfunctions, leading to operational disruptions and costly repairs.
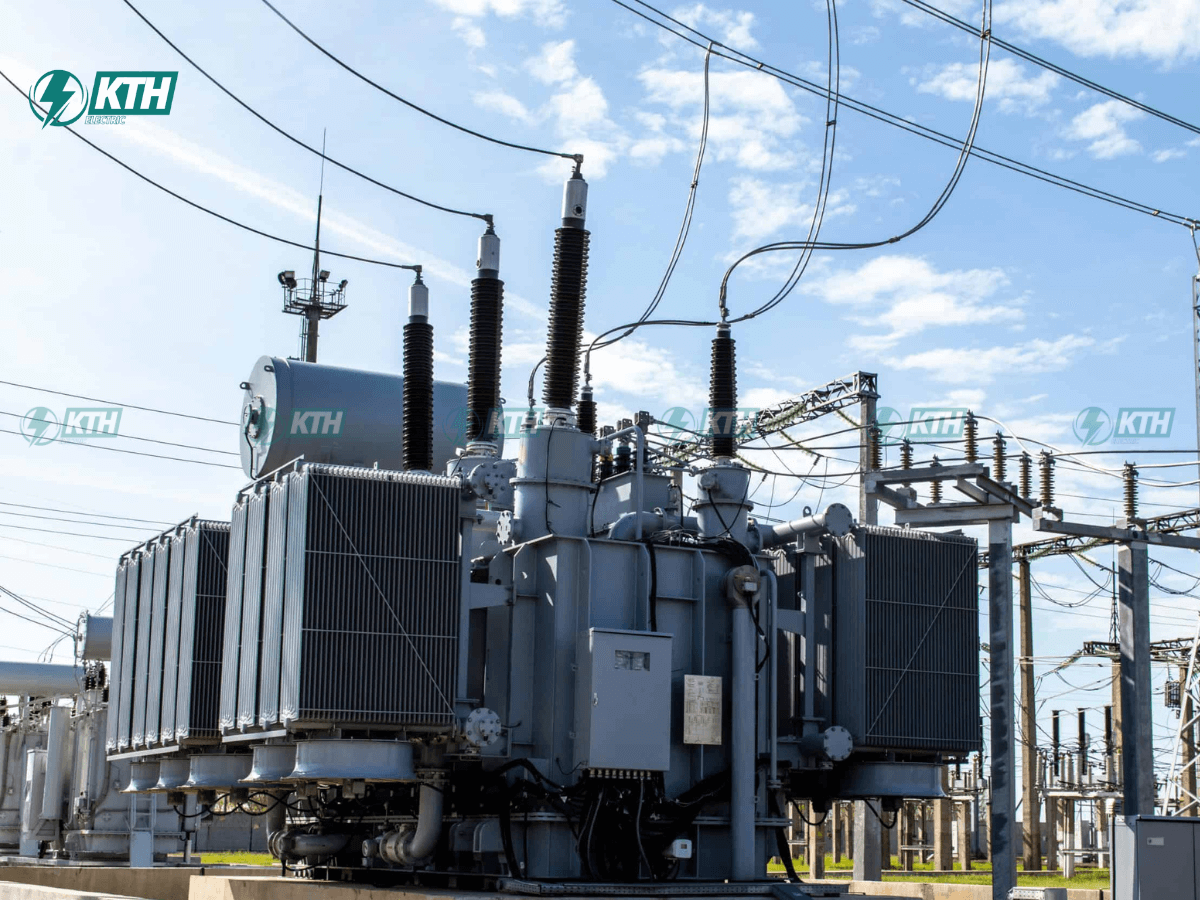
KTH Electric’s industrial transformer station with modern outdoor design ensures reliable power distribution.
With over a decade of experience in industrial electrical systems, KTH ELECTRIC offers comprehensive transformer station maintenance services, ensuring safe and efficient operations for your system.
Transformer Station Maintenance Process at KTH ELECTRIC
We provide maintenance services for oil-filled and dry transformers with a detailed process to ensure safe and efficient operation. Below is the specific maintenance process:
Task | Oil-Filled Transformer Maintenance | Dry Transformer Maintenance |
---|---|---|
1. General Inspection | Analyze and evaluate the transformer’s operational condition. | Analyze and evaluate the transformer’s operational condition. |
2. Professional Cleaning | Comprehensive cleaning of the transformer. | Comprehensive cleaning, including high voltage, low voltage, magnetic core, and cooling fan sections. |
3. Cable and Connection Check | Clean and tighten high and low voltage cable connections. | Inspect high and low voltage cables and the core for signs of burning or damage and clean thoroughly. |
4. Insulation Check | Measure insulation resistance between components: HV-shell, HV-LV, and LV-shell. | Measure insulation resistance between components: HV-shell, HV-LV, and LV-shell. |
5. Oil System Maintenance | Periodically test oil samples, monitor oil temperature, and replenish with the correct oil type if low. | Not applicable. |
6. Shell Cleaning and Porcelain Inspection | Clean the transformer shell and inspect primary and secondary terminals. | Not applicable. |
7. Temperature and Controller Check | Check the operation of the temperature controller and cooling fan controller. | Monitor operating temperature, temperature controller, and cooling fan. |
8. High Voltage Testing (if required) | Perform high voltage dielectric tests to ensure safety. | Perform high voltage dielectric tests to ensure safety. |
9. Reinforcement and Operational Advice | Reinforce the station’s foundation for stable transformer operation. | Reinforce the station’s foundation and provide operational advice. |
10. Control Panel Check | Clean the control panel, inspect circuit boards, and check AC/DC power supplies. | Not applicable. |
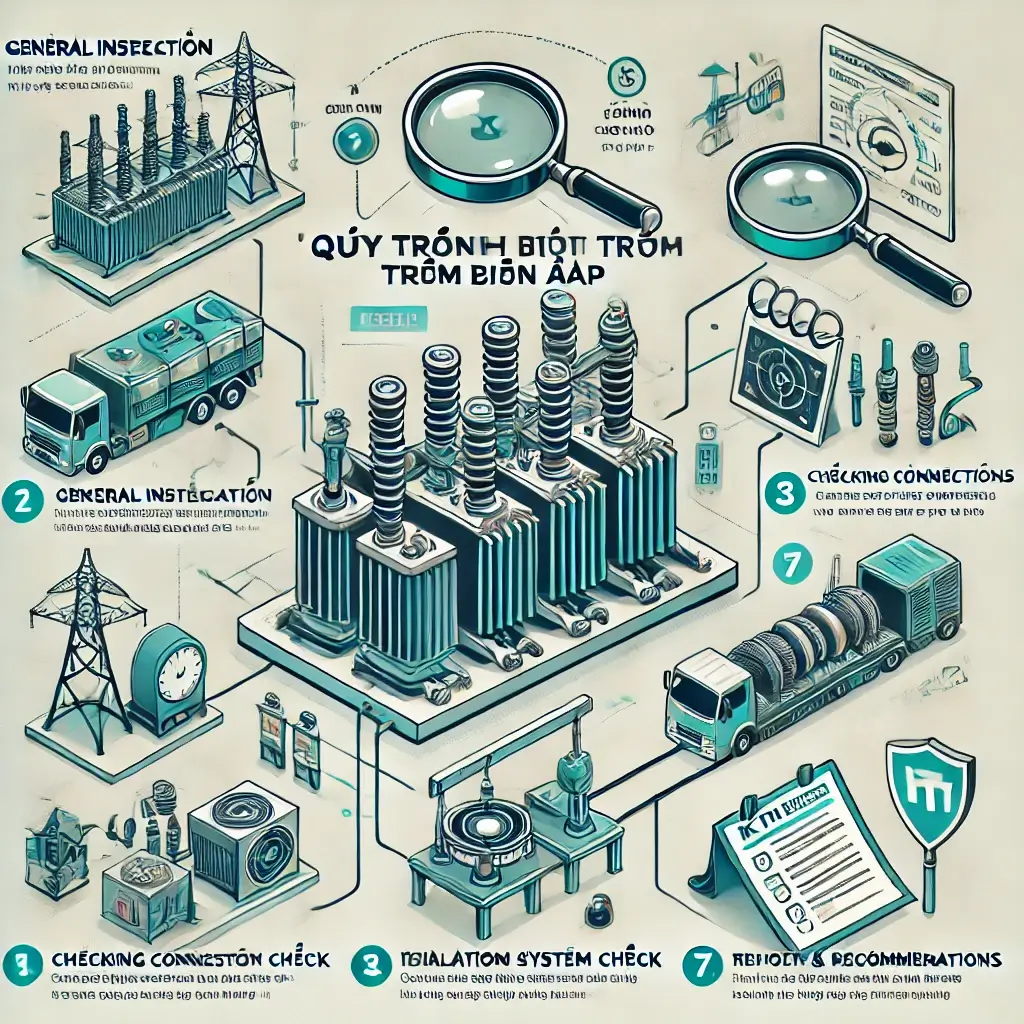
Detailed transformer station maintenance process: From inspection to reporting, ensuring comprehensive care and operational efficiency.
We follow technical standards to conduct a comprehensive inspection of all transformer station components, identifying potential issues early. Below is a maintenance process for 110kV transformer stations we provide:
Component | Maintenance Task |
---|---|
110kV Surge Arrester | Measure insulation resistance, leakage current, inspect grounding system, check connections, and clean industrially. |
110kV/0.11kV Voltage Transformer | Measure insulation resistance, transformer ratio, inspect secondary circuit connections, and clean industrially. |
110kV Isolator | Measure insulation and contact resistance, check control circuits, improve contacts, and clean industrially. |
SF6 Circuit Breaker, 110kV | Measure insulation resistance, operating time, inspect control circuits, improve contacts, and clean industrially. |
110kV Current Transformer | Measure insulation resistance, transformer ratio, assess errors, inspect secondary current circuits, improve contacts, and clean industrially. |
110kV Support Insulator and Ground Switch | Measure ES insulation and contact resistance, inspect connections, and clean industrially. |
110kV/6.6kV, 9.6MVA Transformer | Measure insulation resistance, transformer ratio, check oil levels, address leaks, replace silica gel (if needed), and clean industrially. |
Oil Sample Testing | Conduct chemical and dissolved gas analysis to evaluate insulating oil quality. |
Voltage Regulating Relay | Test characteristics, inspect control circuits, and clean industrially. |
Protective Relay | Check differential protection, overcurrent relays, and trigger circuit breaker testing at both transformer ends. |
Grounding System | Measure grounding resistance, inspect connections, and ensure the system meets safety standards. |
Note: The process can be customized according to client requirements and specific system specifications.
Benefits of Choosing KTH ELECTRIC’s Transformer Station Maintenance Services
- Absolute safety: Ensure no electrical risks, protecting personnel and company assets.
- Cost optimization: Regular maintenance minimizes the need for major repairs and extends equipment lifespan.
- Comprehensive services: Beyond maintenance, we offer energy optimization and system operation solutions.
- Fast support: Technicians are available immediately upon request, ensuring prompt resolutions.
Factors Affecting Transformer Station Maintenance Costs
Maintenance costs depend on factors such as:
- Type of transformer station: Oil-filled or dry transformers have different technical requirements.
- System capacity: Ranges from 100kVA, 500kVA to 1MVA or larger.
- Equipment condition: Older or damaged stations may incur higher repair and replacement costs.
Reference Price Table:
Transformer Station Type | Regular Maintenance Cost |
---|---|
100kVA capacity | From 10,000,000 VND |
500kVA capacity | From 20,000,000 VND |
1MVA capacity | Contact for pricing |
Contact us for a detailed quote tailored to your needs.
Frequently Asked Questions about Transformer Station Maintenance
1. How often should a transformer station be maintained?
- For industrial systems, maintenance is